Portada.Historia.Tecnología.Sociedad.Enlaces
9.
Cochura
La cochura tiene por objeto endurecer las piezas
de arcilla cruda, haciéndolas resistentes y vitrificándolas
para que puedan conservar indefinidamente su forma. Esta operación
se efectúa sometiendo el material a temperaturas elevadas, en hornos
construidos a propósito. La arcilla cruda pierde el agua, se endurece,
adquiere consistencia y se vuelve insoluble por la acción del calor;
sufre un cambio completo en su composición, cambio que depende de su
fusibilidad y se convierte en un ladrillo vitrificado.
Entre los gases que se producen durante la cochura,
el ácido carbónico, el vapor de agua y el nitrógeno,
son los más indicados para determinar cambios en la arcilla. El oxígeno,
óxido de carbono, hidrocarburos e hidrógeno actúan muy
intensamente sobre la mayor parte de cuerpos, aun a baja temperatura.
Reciben el nombre de
combustibles los cuerpos que al combinarse con
el oxígeno del aire producen luz y calor. Una reacción química
desarrollada en esta forma se llama
combustión.
Los combustibles empleados en las tejerías son:
la paja, la madera,
la turba, el lignito y la hulla.
En algunas regiones agrícolas se emplean, como combustible,
pajas
de todas clases en los hornos de tejerías que funcionan periódicamente.
La combustión de la paja requiere una gran vigilancia y un trabajo
continuo, a fin de que no se apague el fuego.
La leña era antiguamente el combustible más usado
y hoy día sigue utilizándose en los países poblados de
bosque; en cambio, en las otras regiones, se va reduciendo el consumo de
leña y es sustituida por el carbón. Las maderas dejan un pequeño
residuo de cenizas, 0,50 a 0,75 %, y desarrollan al quemarse de 3.400 a 4.000
calorías. La madera recién cortada contiene (según las
clases y condiciones) 40 % de agua; secada al aire encierra sólo un
20 %.
La turba se emplea con éxito en las tejerías. Su
ponencia calorífica varía con los vegetales que han contribuido
a su formación. Por la misma causa es también variable el residuo
de cenizas, que oscila entre 16 y 30 % así como el agua que contiene,
si bien ésta importa, por regla general, el 1 1/2 %. Con la turba se
forman panes, aumentando así la potencia calorífica que oscila
entre 4.000 y 4.800 calorías por kilogramo.
El lignito es el combustible más empleado actualmente en
las tejerías de Europa central. Las clases de lignito son tan variables
como su valor. Es, pues, muy conveniente probar el lignito, antes de comprarlo,
determinando la cantidad de cenizas y agua que contiene. Las clases inferiores
se mejoran fabricando panes, si bien sólo pueden pagarse a precios
moderados.
Los elementos que componen el lignito son muy variables. Con frecuencia
contiene un 48 % de materia terrea y 60 % de agua. Un almacenaje prolongado
reduce el agua al 30 y hasta al 20 %. Contiene muchas veces 10 % de cenizas.
Los lignitos de Bohemia son muy apreciados. Arden formando una llama muy
larga y desarrollan una temperatura elevada. De todos modos es siempre recomendable
el probar las muestras antes de adquirir una partida. El número de
calorías oscila entre 4.900 y 5.500.
Las hullas son el mejor combustible que posee la industria. El
mercado ofrece diversas clases, no todas del mismo valor. Existen, entre
otras, hullas bituminosas, hullas de gas, hullas llamadas de negro de humo,
de llama, arenosas, vitrificadas, etc. Tienen por término medio 3
a 8 % de agua, 4 a 30 % de cenizas (si bien éstas oscilan entre el
9 y 12 %). La potencia calorífica es de 6.000 a 8.000 calorías.
El
rendimiento calorífico de un combustible disminuye con
su
grado de humedad. El agua es no sólo inútil, sino
perjudicial. A veces los combustibles se humedecen ligeramente para eliminar
el polvo. Conviene quemar las hullas cuanto antes, para evitar que un almacenaje
prolongado las oxide y pierdan potencia calorífica.
Los gases producidos al quemarse un kilo de carbono constan de una mezcla
de 3,66 de anhídrido carbónico y 8,93 de nitrógeno. Esta
mezcla absorbe las 8.140 calorías desarrolladas por la combustión.
Un kilogramo de anhídrido carbónico necesita 0,216 calorías
para elevar un grado su temperatura y uno de nitrógeno necesita 0,244
calorías.
Combustibles gaseosos.—
Cuando han de cocerse mercancías que conviene salgan del horno
con una coloración limpia se utiliza el gas como combustible. Los gases
más empleados, con este objeto, son: el de agua, fabricado con los
aparatos Strache o el obtenido en gasógenos de carbón. Los
combustibles gaseosos poseen innumerables ventajas y cada día aumenta
su empleo. Con ellos desaparecen las partículas volátiles debidas
a las cenizas y las escorias; las llamas son ricas y poco densas; el servicio
es más uniforme; la temperatura puede regularse con mucha facilidad
abriendo o cerrando las válvulas de entrada de gas y finalmente los
ladrillos no se enfrían tan rápidamente.
10. Clasificación de
los hornos empleados en las tejerías
HORNOS CORRIENTES
Las evoluciones sufridas por los hornos de cocer ladrillos y objetos de
arcilla empleados en la edificación, datan de muchos siglos atrás
y su estudio constituye una parte de la historia de la cerámica. Los
trabajos de investigación y los perfeccionamientos realizados demuestran
el espíritu infatigable de sus autores. Entre estos inventos descuella
el horno circular de
Hoffmann, que representa el progreso mayor realizado
en este terreno y continúa hoy siendo el modelo de todas las instalaciones
de fuego continuo. Otra adquisición del siglo pasado son los hornos
de gas que, por sus excelentes servicios, se emplean cada vez más.
Nuestro trabajo quedará circunscrito a.los hornos empleados más
corrientemente, ya que este manual estudia sólo las instalaciones que
estando actualmente en uso, funcionan con resultado satisfactorio. Prescindiremos,
pues, de consideraciones de orden puramente histórico o científico
y trataremos el asunto sólo desde el punto de vista estrictamente práctico.
Los hornos pueden ser de
servicio continuo o de
servicio intermitente.
Entre los hornos de servicio intermitente o periódico se cuentan
los siguientes.
Los de hogar ordinario con emparrillado, lo mismo si son abiertos, como
cerrados, esto es, abovedados. Estos últimos pueden ser horizontales
o verticales. Se incluyen además en este grupo los tipos de
hornos,
ya anticuados, en que el material se distribuye en dagas.
Describiremos a continuación únicamente aquellos hornos que
están en uso y los que todavía se construyen en explotaciones
muy pequeñas o bien para elaborar mercancías especiales.
El
horno alemán es muy sólido, la cara superior es
abierta y tiene en las longitudinales aberturas para avivar el fuego, que
se prolongan en el interior y conducen los productos de la combustión.
Estas aberturas forman unos hogares que carecen de rejilla cuando se emplea
leña. Si el combustible empleado es el carbón poseen entonces
emparrillado. Las dos caras frontales tienen dos puertas, colocadas a distinta
altura, que sirven para la carga y descarga de los ladrillos. Estos hornos
consumen una cantidad .extraordinaria de combustible, las mercancías
salen de ellos muy limpias y son hoy empleados en Holanda, donde siguen construyéndose
todavía.
Dimensiones del horno alemán
COMBUSTIBLE
|
Ancho
del horno
|
Anchura
del conducto de humos cm
|
Ancho
en medio del hogar cm
|
Ancho
al final del hogar cm
|
Altura
náxima del horno m
|
|
con un hogar m
|
con dos hogares m
|
Leña
|
4,0
|
8,0
|
50-65
|
120-135
|
60-68
|
5,0
|
Turba
|
3,5
|
7,0
|
40-55
|
100-125
|
50-63
|
4,5
|
Lignito
|
3,5
|
6,5
|
35-45
|
95-110
|
48-55
|
4,5
|
Hulla
|
3,0
|
5,5
|
30-40
|
65-95
|
33-48
|
3,5
|
Los hornos alemanes se recubren a veces con una bóveda de
arcilla u otro material, provista de orificios de 15 cm
2 que sirven
para dar salida a los gases o conducirlos a una chimenea común.
Fig. 39.— Horno de Cassel. Estos hornos son
siempre preferibles a los abiertos, pues economizan la tercera parte de combustible.
Los
hornos de llama de Cassel, llamados también
hornos de Cassel, son muy empleados y se pueden utilizar para cocer
ladrillos finos o de revestimiento. El combustible se quema, sobre el emparrillado
d de un hogar, separado por completo de la mercancía (fig.
39). La combustión se regula variando la entrada de aire en el hogar,
ya sea valiéndose de las aberturas
c que con él comunican
o bien cerrando más o menos el registro
i de la chimenea. Valiéndose
de estos medios se reduce el tiempo necesario para la cochura y se economiza
combustible. El hogar ocupa poco sitio y sus dimensiones no dependen de las
mercancías que se cuecen. El calor de la combustión y el cedido
por la llama que horizontalmente atraviesa el horno
f, antes de elevarse
por la chimenea, cuece las mercancías. El hogar tiene dos o tres entradas
de aire. La entrada
g de las mercancías está situada
cerca de la chimenea. Un horno Cassel tiene una capacidad para 15.000 y hasta
30.000 ladrillos. Generalmente se construyen dos hornos juntos, separados
entre sí por una pared y se encienden alternativamente (fig. 40).
Fig. 40. Acoplamiento de dos hornos Cassel.
Un horno Cassel de una capacidad para 15.000 a 17.000
ladrillos, necesita:
Un fogonero y dos peones en cada horno para colocar los ladrillos
y transportarlos; un fogonero para alimentar el hogar y otro para conducir
el fuego; un fogonero y dos peones para sacar los ladrillos del horno.
El tiempo necesario para una cochura se reparte como
sigue:
para colocar los ladrillos y cerrar la puerta de entrada......................1
1/4 días
encender, cocer y apagar................................................................3
»
para enfriarse el material según sean las condiciones atmosféricas.....3
1/2 a 5 »
para descargar el horno...................................................................1
»
duración mínima de una cochura ...............................................
8 1/4 »
» máxima de
una cochura ................................................
10 »
» media de
una cochura ...................................................
9 1/2 »
Quemando carbón de piedra se necesitarán de 80 a 90 hectolitros
de hulla y 240 hectolitros de lignito.
Las dimensiones de un horno Cassel dependen del combustible empleado. Las
mínimas son de 2,3 x 5 m y corresponden a la hulla.
Hornos de llama de retorno.—
En estos hornos los productos de la combustión están separados
de los ladrillos que se cuecen. La llama del hogar se levanta verticalmente
hasta chocar con la bóveda del mismo y toma luego una dirección
de arriba abajo para salir por los conductos de abducción distribuidos
uniformemente bajo la solera del horno. Los hogares están separados
de la cavidad del horno por unos muros que sirven, al mismo tiempo, para
dar dirección a la llama.
Esta clase de hornos gastan mucho combustible y únicamente se emplean
para cocer ladrillos recochos, baldosas, mercancías esmaltadas, tejas
finas, tubos esmaltados, ladrillos de revestimiento y en general mercancías
finas. La temperatura máxima está en las dagas superiores, que
son las menos cargadas; mientras que las dagas inferiores están sometidas
a una
cochura más uniforme a elevada temperatura; razón
por la cual no se alabean a pesar de estar más cargadas. Estos hornos
pueden acoplarse y se colocan a veces varios en serie para no interrumpir
la cochura.
Existe una gran variedad de hornos de llama de retorno, conocidos con los
nombres de
hornos redondos y
hornos angloamericanos, que se
utilizan en las alfarerías y fábricas de loza y porcelana. Estos
hornos acostumbran a construirse de varios pisos.
Los hornos de mufla son completamente cerrados y se hacen de arcilla
refractaria. Los objetos que han de cocerse se colocan en el interior de la
mufla y ésta se dispone en un horno rectangular de ladrillo, en forma
que las llamas puedan envolverla completamente. En las fábricas de
objetos de arcilla destinados a la edificación, se emplean hornos de
mufla de diversos tamaños para cocer artículos finos, como son
azulejos, tejas mecánicas, trabajos de mayólica, etc.
Augustin, el famoso especialista en la elaboración de ladrillos
de revestimiento, ha construido un
horno de mufla, muy práctico,
en el que se utiliza el gas como combustible. La planta del horno
es rectangular y tiene en la dirección de su longitud, dos canales
de combustión, separados entre sí por una gruesa pared. Cada
uno de estos canales está dividido en seis departamentos, por unos
tabiques de cinco centímetros de espesor. Los departamentos situados
en uno de los extremos de los canales, son mayores que los restantes. En cada
departamento hay tres hogares, construidos con tabiques de cinco centímetros
y recubiertos además por debajo de la bóveda general. Las cámaras
mayores poseen cuatro hogares. Cada departamento tiene una llave de gas en
la parte exterior del horno, abierta, la cual pasa el gas al conducto correspondiente
a dicho departamento. De este conducto sale un tubo para cada hogar, tubo
que se divide en dos para alimentar a los tubitos que forman el hornillo de
gas. El aire para la combustión procede de otro sistema de tuberías
y se calienta previamente en los departamentos que dejara de funcionar. Al
quemarse el gas se levantan dos gruesas llamas, que bajando por los conductos
laterales pasan por. los centrales a los conductos de abducción, situados
baje la solera del horno.
Hornos para colorear tejas.—
En muchas regiones se prefieren tejas azules, grises o de tonos acerados
a las ordinarias. Estas coloraciones se obtienen fumigando las piezas después
de la cochura.
Antiguamente se quemaban, con este objeto, hojas tiernas o ramas verdes,
que una vez terminada la cochura, se echaban al horno en paquetes ya preparados.
Cargado así el horno se cerraba herméticamente. Hoy día
se quema aceite de oliva, petróleo en bruto o alquitrán para
producir el humo cuyas partículas se depositan luego sobre las tejas.
Los resultados obtenidos son tanto mejores, cuanto mayor es la temperatura
de las tejas.
Los hornos empleados para fumigar son intermitentes y tienen uno o dos fuegos
en las dos caras frontales. En este último caso los conductos de abducción
parten del centro de la solera. El fuego se hace en
hogares construidos
en forma que queden protegidas las mercancías que se están cociendo.
En la parte anterior de los hogares hay unos agujeros para colocar los embudos
que sirven para echar el aceite. Sobre la bóveda del horno se coloca
una gruesa capa de arena, que ha de mantenerse húmeda mientras se
produce el humo necesario para colorear. El horno permanece cerrado herméticamente,
no sólo durante el tiempo en que se producen los vapores coloreantes,
sino además, todo el necesario para enfriar la mercancía; pues
de lo contrario, las partículas carbonosas depositadas en los poros
de las tejas se encienden y se queman, desaparece el color negro y queda un
tono sucio que hace invendibles los artículos.
Entre los
hornos destinados a pruebas de cochura, son muy generalizados
los de
Seger, de Berlín, y el de
Loeser, de Halle (figura
41). Este último es un horno de gas de doble llama de retorno y conductos
de abducción bajo la solera.
Fig. 41.— Horno de ensayos, de Loeser.
El gas producido en el gasógeno pasa por delante
los hogares a través de conductos dispuestos en los muros exteriores
del horno. Algo más bajos que éstos hay otros canales, que conducen
aire al hogar. Aire y gas mezclados se encienden, formando llamas que se
esparcen por todo el horno. Los productos de la combustión salen por
unos canales dispuestos bajo la solera y calientan el aire que, en sentido
contrario, pasa por unos tubos montados en dichos canales. Este aire, así
recalentado, es el empleado para alimentar la combustión.
HORNOS DE SERVICIO CONTINUO
ACANALADOS
Los hornos de servicio continuo han convertido la elaboración de
ladrillos en una industria, y permiten fabricar material en grande escala.
Hace unos ochenta años que se construyen estos hornos, y desde entonces,
es posible calcular la producción diaria de una tejería y fabricar
una cantidad determinada de ladrillos.
Los hornos continuos pueden ser de dos clases: 1.ª de hogar fijo; 2.ª
con fuego móvil, que avanza a medida que adelanta la operación.
A la primera corresponden los hornos acanalados.
Fig. 42.—Alzado de un horno de canal.
Los hornos acanalados se construyeron por vez
primera en 1840 y son de hogar fijo y solera móvil. Yordt,
de nacionalidad danesa, fue el inventor; pero hasta 1875 en que Otto Bock
construyó un horno acanalado de condiciones industriales no tuvieron
aceptación en el terreno de la práctica. Actualmente Moeller
y Pfeiffer utilizan los hornos acanalados como secaderos con calefacción
artificial (fig. 42).
Los hornos acanalados se caracterizan, como su nombre lo indica, por su
forma larga de canal y tienen el hogar colocado en la mitad del horno,
desde donde los productos
de la combustión van a parar a la chimenea colocada en un extremo
del horno. Los ladrillos, cargados en vagonetas, entran en el horno por este
extremo y, siguiendo una dirección contraria a los gases, avanzan lentamente
y llegan al hogar calentados y humeantes. Allí acaban de cocerse y
sigue la vagoneta su vía, hasta salir por el extremo opuesto con los
ladrillos bastante enfriados.
Hacía años que los hornos acanalados habían caído
en desuso y nadie se acordaba de ellos, hasta que Moeller y Pfeiffer
los emplearon de nuevo para combinarlos con los secaderos. Esta combinación
permite una doble utilización del calor y no se necesita calefacción
especial para los canales del secadero, gracias a un sistema de condensación
que permite recuperar, en el secadero, el calor contenido en el vapor de escape
de la máquina de vapor.
Explotación de una tejería
de hornos y secadero acanalados.—
Un montacargas inclinado eleva la arcilla al cuarto de prensas. Allí
es prensada, y los ladrillos recién moldeados se cargan en las vagonetas
del secadero por medio de unos platos giratorios. Cada vagoneta lleva 250
piezas y tarda de 17 a 24 horas para recorrer completamente el secadero.
Al salir de éste, las piezas se trasladan a las vagonetas del horno
y se carga cada una con 700 ladrillos. Se necesitan, pues, tres vagonetas
del secadero por cada vagoneta del horno. Las vagonetas vacías vuelven
al cuarto de prensas y las cargadas vuelven al horno. Allí avanzan
automáticamente, empujadas por prensas hidráulicas o de ruedas
dentadas, que distribuyen el tiempo necesario para la cochura entre la longitud
del horno. La cochura tiene lugar, como en los hornos circulares, por medio
de fuego distribuido uniformemente, y los ladrillos ya cocidos son trasladados
en las mismas vagonetas al almacén y allí se depositan o bien
se expiden (fig. 43).
HORNOS CONTINUOS DE FORMA ANULAR
Las pruebas realizadas con el fin de aprovechar el calor de los hornos por
medio de una combustión continuada, datan del siglo XVIII. Müller
presentó en 1776, al Ministerio real de Obras Públicas de Berlín,
el plano y la memoria descriptiva de un horno ideado por él, en el
que se reducía el consumo de leña a la mitad.
Fig. 43.—Sección transversal de un horno
acanalado: a, a, cierres de arena para incomunicar las partes superior e inferior
de la vagoneta; d, d, via interior; e, e, via exterior.
Constaba dicho horno de seis unidades, construidas una junto a otra. Arnold
proyectó en 1839 un horno formado por siete departamentos construidos
alrededor de una chimenea central. Hallmann patentó en 1854
un horno circular. Pero el horno circular propiamente dicho, el que mejores
servicios ha prestado en las tejerías, el que abre una nueva época
en la tecnología de nuestra industria, es el ideado por el maestro
real de obras Federico Hoffmann, de Berlín. El primer horno
circular fue construido en Stettin en 27 de Mayo de 1858 y durante nueve
años los resultados no fueron muy satisfactorios. En 1865 el gremio
de ladrilleros alemanes recomendó el empleo de estos hornos. En Austria
fue construido el primer horno circular por Enrique Drasche, a la
sazón el fabricante más poderoso de la monarquía. Muy
pronto otros fabricantes imitaron a Drasche y construyeron hornos
circulares del tipo Hoffmann, análogos al levantado por Drasche
en Wienerberg. El horno circular ha sido la mejor adquisición de las
tejerías. Hoffmann utilizó los mismos ladrillos que
habían de cocerse para formar el hogar, de modo que las piezas crudas
y el combustible estaban mezclados en el interior del horno.
Horno anular de Hoffmann.—
Los primitivos hornos de Hoffmann eran redondos, abovedados y con
puertas de trabajo distribuidas uniformemente en la circunferencia exterior
de la planta (fig. 44). Frente a estas puertas y en número igual a
ellas hay los canales de abducción, que terminan en un conducto
general de humos que comunica, por medio de cuatro aberturas, con la
chimenea construida en el centro del horno.
Fig. 44.—Planta del primitivo horno Hoffmann.
Los canales de abducción se cierran desde
el exterior del horno, valiéndose de unos registros en forma de campana.
Sobre la bóveda del horno hay distribuidos una serie de agujeros
para avivar el fuego, que se cierran con tapones de hierro. En sentido
radial hay, dentro del horno, unas ranuras que sirven para sostener las planchas
de hierro correderas destinadas a dividir el horno en compartimientos. El
número de compartimientos es igual al de puertas de trabajo. Actualmente
las correderas se hacen de cartón y son muy reducidos los ejemplares
de hornos iguales al descrito.
El horno anular moderno es oblongo (fig. 45), formado por dos cámaras
laterales unidas entre sí por otras dos semicirculares. La chimenea
no se construye en el centro del horno, sino a un lado, separada del mismo,
y puede servir para dos o tres hornos a la vez. La misma chimenea se utiliza,
a veces, para el tiro de las calderas de vapor.
Fig. 45.—Planta de un horno anular oblongo.
Los departamentos de los hornos oblongos son rectangulares,
en su mayoría, y en ellos pueden disponerse los ladrillos mejor que
en los departamentos circulares del horno antes descrito. La distribución
del fuego es más uniforme en un departamento rectangular. Tienen estos
hornos unos pocos departamentos de planta en forma de sector, los cuales
pueden funcionar del mismo modo que los del horno redondo, si los agujeros
para avivar el fuego se han distribuido con acierto. El tejado que cubre
los hornos oblongos es de construcción mucho más sencilla que
el de los hornos primitivos.
El combustible se echa por los tubos colocados en la bóveda del horno
y al caer entre los ladrillos incandescentes aviva el fuego. La parte encendida
de horno forma una especie de retorta, donde el combustible, al caer, desprende
gases, que se encienden al contacto del oxígeno disponible en el interior.
Esta reserva de oxígeno mantiene a su vez incandescente el residuo
de cok. El calor avanza comunicándose de un departamento a otro, y
cuando los ladrillos correspondientes a un agujero están incandescentes,
puede echarse combustible en el mismo.
El combustible se echa a intervalos de tiempo muy cortos; lo mejor es disponer
de un reloj que dé una llamada cada cinco minutos. No se crea que
la combustión avanza diariamente de un departamento; esto es, que
durante todo el día arda el fuego en un compartimiento del horno y
pase repentinamente la combustión al próximo cuando empieza
la nueva jornada de trabajo. Precisamente la idea fundamental del horno circular
es obtener un avance lento y progresivo de un metro en cuatro a seis horas,
aproximadamente. Si quiere trabajarse con más lentitud puede reducirse
este avance a dos metros en veinticuatro horas; al contrario, puede avanzarse
de siete a ocho metros en el mismo tiempo, si quiere acelerarse la cochura.
Los días festivos o bien cuando faltan ladrillos crudos se interrumpe
la cochura cerrando herméticamente el horno, de modo que no pueda
entrar ni salir aire; al cabo de algunos días pueda continuar la combustión.
A veces únicamente se aviva el fuego durante el día y por la
noche se conserva incandescente el horno sin avanzar el fuego.
Aun cuando la parte de horno comprendida entre dos puertas de trabajo recibe
el nombre de
departamento, debe advertirse que sólo transitoriamente
permanece separada del resto del horno. Este nombre responde tan poco a la
realidad como el llamar
corredera a la pared de papel que por cierto
tiempo separa dos cámaras entre sí.
La producción diaria de un horno circular depende de la sección
de la cámara; en cambio el número de departamentos no influye
en la producción. Este número no pasa de catorce a diez y seis;
si bien
Hoffmann construyó en Wienerberg, junto a Viena, por
orden de
Drasche, hornos dobles, de doble cámara y con treinta
y dos departamentos.
El tamaño de un departamento o sea el número de divisiones
del horno depende de la cantidad de ladrillos elaborados diariamente. Al
hacer el cálculo pueden contarse trescientos días de trabajo
para las tejerías que fabrican todo el año y sólo doscientos
para aquellas que trabajan únicamente durante el verano y la primavera.
A una producción anual de dos millones de ladrillos corresponden (suponiendo
trescientos días de trabajo) un promedio diario de 6 2/3 millares
de piezas elaboradas. Cada departamento del horno deberá tener, pues,
una capacidad suficiente para 6 1/2 ó 7 millares de piezas.
Hoffmann resume las
ventajas de su horno circular en los puntos siguientes.
1. El horno anular está protegido
contra la humedad del suelo por medio de una capa aislante que lo separa
por completo de la fundación. Un tejado le protege de las lluvias.
2. Un grueso de arena u otro material análogo, cubriendo
el horno, evita la irradiación de calor.
3. El calor emitido por los ladrillos al enfriarse sirve
para facilitar la propagación del fuego y aumenta, al mismo tiempo,
su acción.
4. Del mismo modo, el calor desprendido por las paredes
del horno al enfriarse es un auxiliar de la combustión.
5. Los gases de la combustión, antes de salir, recorren
todo el horno, cediendo calor a los ladrillos que han de cocerse y preparándolos
para la combustión.
6. El fuego adelanta a intervalos de
tiempo muy pequeños y los ladrillos que han de cocerse entran lentamente,
unos tras otros, en contacto con la llama, el fuego se acerca a ellos cada
vez más y acaban por formar más tarde parte del mismo. Con
este procedimiento el calor se aprovecha en las condiciones más favorables
y se consigue una gran economía de combustible, que asciende al 60
ó 70 % respecto al total consumido por los hornos antes descritos.
El horno circular gasta de 100 a 150 Kg de carbón de piedra por mil
ladrillos cocidos, según sean las dimensiones de éstos.
Los gastos de explotación son menores, por las razones siguientes:
1. la conducción del fuego es fácil
y sencilla, bastando una inspección cuidadosa;
2. el trabajo de carga y descarga es el mismo cada día
y los operarios lo aprenden fácilmente;
3. los hornos circulares son bajos y por consiguiente la
colocación de ladrillos es una operación mucho más sencilla
en estos hornos que en los ordinarios, donde los rejales alcanzan hasta cuatro
metros de altura.
En los hornos circulares sólo hay peligro de incendio si el fogonero
es tan descuidado que acumule una cantidad excesiva de combustible hasta
pegar fuego sobre la bóveda.
La propagación del incendio es de todos modos muy difícil,
pues los operarios que necesariamente han de vigilar el horno para ir conduciendo
el fuego tienen tiempo de acudir a la extinción.
Son necesarias muy pocas reparaciones y las pocas que se presentan pueden
hacerse sin interrumpir el servicio.
El coste de estos hornos es pequeño relativamente a la producción.
El coste del horno se reparte del modo siguiente, poco más o menos:
1 1/2 % en desmontar el terreno y rellenar,
15 » »
jornales de albañil,
35 » »
el coste de los ladrillos,
5 » »
material (cemento, cal, arcilla refractaria),
20 » »
madera y trabajos de carpintería,
10 » »
el material de recubrimiento y jornales,
7 » »
piezas de fundición,
6 1/2 » » gastos de
inspección e imprevistos.
Las fundaciones y el relleno de los muros pueden hacerse con mampostería.
La chimenea puede construirse dentro o fuera del horno. Esta última
disposición es cara y sólo puede aconsejarse cuando el terreno
es seco a mucha profundidad, pues el canal de unión entre la chimenea
y el conducto general de humos va a parar muy bajo.
El
horno circular fraccionado que representa la figura 46 es de construcción
análoga a la del horno anular y sólo se distingue de éste
en ser una fracción del mismo. Se construye donde un horno anular
no resultaría económico o bien cuando se piensa completarlo
más tarde. La cámara del horno tiene varios departamentos (de
tres a ocho), donde sólo se entra por las puertas de trabajo colocadas
al exterior, y comunica por uno de sus extremos con un hogar provisto de
emparrillado, igual al del horno de Cassel, y por el otro extremo con el
conducto de humos que la une a la chimenea. Al construir el horno se hacen
agujeros en la bóveda y se construyen los conductos de abducción
que prestarán servicio más tarde o sea cuando se complete el
horno.
Este horno, a pesar de su analogía con el horno anular, es de servicio
intermitente. Para encenderlo se hace fuego en el hogar colocado en uno de
sus extremos; la combustión adelanta lentamente en dirección
a la chimenea a medida que se echa combustible por los agujeros de la bóveda
y al llegar al otro extremo se deja apagar el horno. Se retiran luego los
ladrillos cocidos y, cargado de nuevo el horno, vuelve a encenderse.
Hay
hornos intermitentes de combustión igual a los hornos circulares;
cuando no se tiene el proyecto de completar el horno, dejan de construirse
los conductos de abducción y en vez de reunir los humos en una pared
transversal se adopta la misma circulación de gases de los hornos
completos y se construye un muro de revestimiento con talud exterior.
Fig. 46.—Alzado de un horno anular fraccionado.
Así se tiene un horno periódico que
únicamente se diferencia del horno fraccionado en el modo de conducir
el fuego; pues la combustión se lleva como en un horno circular ordinario.
El humo en los hornos circulares ocasionaba no pocas dificultades
al principio. En los intermitentes era fácil el dejar que humeasen
los ladrillos, pues bastaba abrir las puertas del hogar y dejar paso al aire
frío hasta secar completamente las mercancías; en cambio los
hornos circulares no podían emplearse para cocer mercancías
finas, y actualmente sólo pueden recomendarse si van provistos de
sistemas adecuados para el humo, o en caso contrario, si los ladrillos se
colocan bien secos en el horno.
Hoffmann, con objeto de aminorar los inconvenientes que se presentaban, construyó
un conducto de humos en la parte superior del horno. Este conducto era circular
y estaba colocado entre el muro interior de la cámara del horno y
la bóveda del colector general de humos. Este método tenía
muchos inconvenientes, pues los gases calientes sólo tenían
salida por los tubos de abducción que estaban destapados. Más
tarde, Hoffmann colocó un segundo conducto, también circular,
en la parte baja del horno, entre los fundamentos exteriores de la cámara
y el muro de revestimiento. Este conducto comunicaba con la cámara
del horno por una serie de aberturas que podían abrirse a voluntad;
cada una de estas aberturas viene a parar en medio del pavimento de la respectiva
puerta de trabajo. Cuando los ladrillos empiezan a humear se abre un orificio
en la puerta tabicada del departamento que se está enfriando, se levanta
el registro del conducto de humos correspondiente a esta puerta y se cierra
la abertura con una plancha, enlodando bien los bordes. Las mismas
operaciones se hacen en el departamento de donde quiere sacarse el humo,
con la sola diferencia de que el boquete no se abre en la parte superior
del tabique, sino abajo, junto a la solera.
Otro procedimiento para dejar que los ladrillos humeen consiste en utilizar
el conducto superior para absorber los gases humeantes, poniéndolo,
con este objeto, en comunicación con la chimenea. En tal caso, el
aire caliente procedente del conducto inferior, atraviesa el departamento
humeante y el humo sale por la chimenea, después de pasar por el conducto
superior.
Para que los ladrillos humeen se utilizan unos hogares especiales que se
montan delante de la puerta de trabajo y sirven el departamento comprendido
entre dos puertas. Otras veces se colocan estos hogares sobre los agujeros
de la bóveda, correspondiente al departamento que está humeando.
Algunas casas constructoras, como Bührer, Bock, Eckardt y otras, han
construido hornos circulares acortados o en zigzag. Estos tipos son de poca
duración y sólo pueden recomendarse donde no se dispone de
espacio suficiente para la construcción de un horno anular o cuando
el terreno no reúne condiciones adecuadas. Estos hornos no son más
que un auxiliar muy caro, por las muchas reparaciones. La única ventaja
estriba en poder construir un horno de cámara muy larga en un espacio
relativamente pequeño; la sección de la cámara es estrecha.
Horno circular de Dannenberg con disposición
para que puedan humear los ladrillos.—
E\ constructor de hornos A. Dannenberg, trabajó desde 1872
en la construcción de disposiciones especiales para humear que tuvieran
un funcionamiento sencillo. Adquirió varias patentes que combinó
más tarde para adoptar finalmente una disposición muy aceptada
en Austria y Alemania.
Los departamentos del horno hasta cincuenta metros cúbicos de cabida,
van provistos de un registro para el humo de los ladrillos y para los gases;
en cambio los departamentos mayores, así como los hornos destinados
a cocer piezas grandes, tienen dos válvulas para que puedan humear
los ladrillos y para los gases. Sólo los registros correspondientes
a los gases de salida, están bajo la influencia de la chimenea, y
por consiguiente, no puede darse el caso que los conductos para humear se
vuelvan permeables. Tiene este horno la ventaja de que los obreros efectúan
la carga y descarga de los departamentos a una temperatura relativamente
moderada, debido a la fuerte corriente de aire que penetra por las puertas
de trabajo. Este aire se calienta en los departamentos más lejanos
y asciende luego a la parte superior, donde primero cede calor al aire que
a través de los agujeros de la bóveda penetra en el horno y
luego pasa por unos canales de mampostería (no de plancha) que lo
conducen al departamento humeante; entra allí por una serie de agujeros
uniformemente repartidos a un mismo nivel y colocados en la parte alta del
departamento, atraviesa éste saturándose de vapor de agua y
sale por los agujeros repartidos en la solera del departamento para escaparse
por la chimenea. En el conducto para humear entra, como hemos dicho, aire
caliente procedente del departamento vacío y al mismo tiempo se extrae
de dicho conducto una cantidad de aire caliente que a través de los
registros semiabiertos se deja entrar a poca presión en uno o dos
departamentos de los que antes se ha extraído el humo por medio de
aire caliente. La cochura dura así menos tiempo, pues los departamentos,
antes de encenderse, se han secado y calentado a cien grados.
El horno anular con conductos de abducción en la parte alta de
la cámara fue construido por vez primera en 1879, por Simohn y
Rost, quienes lo construyeron sin bóveda en Szegedin. Mas tarde,
Bock lo mejoró notablemente y lo introdujo en Alemania (fig.
47).
Este horno consta de dos cámaras unidas entre sí en los extremos
y de un conducto de humos, perfectamente aislado, colocado en la pared de
en medio y unido a la chimenea por uno de sus extremos. Su construcción
es, pues, igual a la de un horno Hoffmann, con conducto de humos en la parte
superior. En el horno de Bock se suprimen las válvulas en forma de
campana, los canales de humear, los registros de regulación y otras
disposiciones del horno Hoffmann. Los productos de la combustión y
el humo, salen por los agujeros colocados en el techo de la cámara
destinados usualmente a avivar la combustión. Dichos agujeros se ponen
en comunicación con el conducto de abducción por medio de tubos
móviles que se colocan en el departamento por donde han de salir los
gases.
Fig. 47.—Horno anular de Boch, sin bóveda.
La ventaja mayor de este horno, está en el avance relativamente
pequeño de la combustión; pues así como en los hornos
con colector inferior, al cerrar una válvula de abducción y
abrir la inmediatamente próxima, el avance de los gases en el interior
de la cámara es igual a la longitud de un departamento, en este horno
de colector superior al trasladar un tubo de abducción de una a otra
serie de agujeros avanza la salida de los gases únicamente una longitud
igual a la distancia entre dos series inmediatas de agujeros y por consiguiente
se entrega al horno una cantidad mucho menor de ladrillos fríos.
Bock cita las ventajas siguientes de los hornos con
conducto de humos superior: una salida perfecta de los productos de la combustión,
sin producirse condensación alguna, y por consiguiente, una gran economía
de combustible; la salida de los gases avanza de una longitud igual al fuego,
pues al echar el combustible por una serie inmediata de agujeros, se traslada
un tubo de escape a otra serie también inmediata; los productos de
la combustión salen sin tocar los ladrillos crudos que están
todavía húmedos, de donde resulta una mayor duración
del horno, una construcción más sencilla y, por consiguiente,
una economía al edificar.
Horno anular sin bóveda de Bock.—
La construcción de hornos anulares sin bóveda no es cosa nueva;
pero esta construcción no se propagó fácilmente, pues
el tipo antiguo de horno anular, con sus dimensiones y puertas de entrada,
tenía mucho arraigo.
Bock adoptó una construccción más económica y
comunicó toda clase de detalles a las asociaciones de fabricantes
de ladrillos.
El horno de Bock es más sencillo. Suprimió las puertas de trabajo,
redujo la altura a una dimensión que permitiera operar fácilmente
y del horno circular sólo adoptó las ventajas que resultan
del servicio continuo.
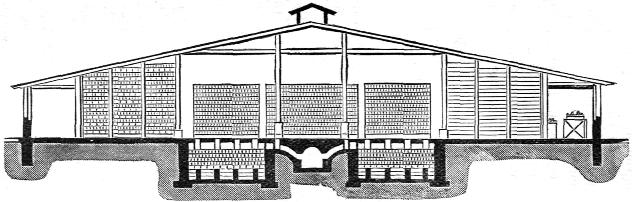
Fig. 48.—Corte longitudinal del horno de Bock.
Este horno no puede tener departamentos por carecer
de puertas de trabajo. En el horno circular ordinario hay siempre abiertas
dos puertas de trabajo para la carga y descarga y con ello se pierde longitud
de horno; en cambio en el horno de Bock no se presenta este inconveniente,
pues carga y descarga se hacen consecutivamente. Además el trabajo
en la cámara de este horno, donde el aire y la luz pueden entrar libremente,
es siempre más sano (figura 48).
El horno anular de Bock necesita mayor cantidad de combustible que un horno
abovedado, a fin de compensar las pérdidas de calor que se producen
a través del techo delgado y móvil; sin embargo, este
calor puede aprovecharse para secar ladrillos. Junto al horno y colocados
en dirección de su longitud se colocan las estanterías del
secadero y detrás de éstas hay un ancho pasillo donde se moldea.
En el corte de la figura 48 puede verse: a la derecha una mesa de moldear,
un banco para colocar los ladrillos recién moldeados y una tabla para
transportar ladrillos; en medio del edificio hay el horno y sobre el techo
plano del mismo se han puesto a secar ladrillos apilados en rejal. Los agujeros
para la carga del combustible se hallan distribuidos en el techo. El horno
anular no está dividido en departamentos, sino en diez y seis zonas.
En las zonas 1 y 2 humean los ladrillos y detrás de ésta hay
la pared divisoria de papel; en la zona 3 se colocan ladrillos, en la 4 entran
vagonetas cargadas, en las zonas 5 a 8 se enfrían los ladrillos ya
cocidos; los ladrillos colocados en las zonas 9 y 10 están todavía
ardientes; en las 10 a 12 se realiza la plena combustión del horno
y en las 15 y 16 empiezan a calentarse los ladrillos. En estas zonas y en
la 1 y 2 están abiertos los registros del conducto de humos. Los ladrillos
recién moldeados se ponen a secar sobre tablitas en las estanterías
colocadas a ambos lados de la cámara del horno. Mesa de moldear, banco
y caballete se colocan delante de la zona 11, donde la combustión
está en su máximo. Cuando deja de echarse combustible en una
serie de agujeros, se colocan, sobre esta línea del horno, los ladrillos
medio secos que ocupan la estantería próxima a ellos, a fin
de que el ladrillero pueda siempre moldear frente a estantes vacíos.
La zona 10 contiene los ladrillos recién moldeados y en cambio la
12 aquellos que fueron moldeados primeramente. Todos los estantes están
ocupados, con excepción de los correspondientes a la zona 11.
El techo del horno y el trozo de pared central correspondientes a las zonas
4 a 11 están cubiertos de ladrillos secos, A medida que avanza la
cochura se van colocando en el horno los ladrillos que hace más tiempo
están almacenados. Por lo demás, el servicio en nada se diferencia
del propio de los hornos circulares.
Cuando estos hornos han de prestar un servicio transitorio es muy conveniente
hacerlos subterráneos, de modo que el nivel superior del techo del
horno venga al nivel del suelo. Sobre el horno se construye un edificio de
ancho suficiente para contener, a cada lado del horno, las estanterías
del secadero y el pasillo de moldear. Las paredes exteriores del horno se
construyen del grueso necesario para sostener una bóveda, de modo
que después de levantadas, cubiertas con la bóveda y construido
un pasillo alrededor quedaría el horno convertido en un horno circular.
Procediendo en esta forma pueden cocerse en un horno sin bóveda los
ladrillos que más tarde serán necesarios para edificar la tejería
y completar el horno circular.
Hornos radiales de Eckardt,—
Esta casa constructora de chimeneas y hornos de Colonia patentó un
sistema de hornos para cocer grandes cantidades de ladrillos y llenar las
exigencias de una gran producción. Este horno se compone de varias
partes o brazos y su número depende de las condiciones del servicio.
Los hornos de esta clase construidos hasta la fecha tienen la planta distribuida
en las formas que esquemáticamente dibujamos a continuación.
Con estos hornos se consiguió centralizar los servicios de las grandes
explotaciones, facilitar su inspección y regular la producción
según las necesidades de momento, sin necesidad de parar el horno.
Uno de los hornos construidos por la casa Eckardt estaba formado por tres
brazos, producía de 18.000 a 55.000 ladrillos diarios y tenía
dos, tres y hasta cuatro fuegos encendidos a la vez; otro horno de los construidos
por dicha casa estaba compuesto de cuatro brazos, tenia tres o cuatro fuegos
y producía de 26.000 a 55.000 ladrillos. Un fogonero sirve los tres
fuegos, tanto si el horno tiene tres como cuatro brazos.
En 1898 Eckardt obtuvo una patente de un sistema de hornos circulares formado
de uno, dos o más pisos con las cámaras de fuego colocadas
una sobre otra.
Los pisos se construyen uno sobre otro, de modo que la bóveda del
uno soporta la carga de ladrillos del horno inmediato superior. En estos
hornos es más sencilla la conducción del fuego y humo y su
construcción es también bastante más económica.
Horno anular de cocer tejas Hotop.—
El horno anular ordinario es poco apropiado para cocer exclusivamente tejas
en grandes cantidades. Un horno anular puede cocer toda clase de piezas (excepción
hecha de las tejas y productos delgados de buena calidad) haciendo sólo
de ladrillos ordinarios las dos dagas inferiores para que sirvan de base
al resto del rejal.
El horno para cocer tejas es un horno anular de cámaras paralelas.
Tiene únicamente de seis a ocho departamentos que se cierran herméticamente
por medio de planchas correderas de hierro. El funcionamiento es igual al
de los hornos anulares, el consumo de combustible algo mayor y su ventaja
estriba en cocer las tejas sin necesitar lecho alguno de ladrillos ordinarios,
que encarecen inútilmente la producción cuando no pueden venderse
en buenas condiciones. El mayor consumo de combustible queda compensado sobradamente
por evitar los perjuicios que ocasiona el inconveniente expuesto.
Hotop
expone las ventajas siguientes.
1. Pueden cocerse tejas de enchufe y planas
de todas clases, así como tubos de avenamiento y artículos
de clase superior, sin necesitarse ladrillos ordinarios, en el supuesto de
que las citadas mercancías puedan colocarse en el horno unas encima
de otras y no necesiten apoyarse sobre obra alguna. La altura ha de ser apropiada
a las cualidades de la arcilla.
2. El consumo de combustible por mil tejas es igual al
de los hornos anulares ordinarios, donde siempre es necesario cocer además,
junto con las tejas, varias dagas de ladrillos para formar la base y proteger
las mercancías.
3. Las mercancías obtenidas son completamente limpias,
debido a que el combustible no está en contacto con ellas durante
la cochura. Esta propiedad del horno permite obtener resultados muy satisfactorios.
4. La pieza se cuece uniformemente y adquiere toda ella
gran dureza sin necesidad de un humeado previo, ni de presión mutua;
debido a que, mejor que en ningún otro horno, puede regularse el combustible,
vigilarse la cochura y observar cómo avanza el proceso de la cocción.
5. El fuego puede avanzar muy rápidamente sin perjudicar
la uniformidad de la cochura.
6. La conducción del fuego en los hornos es mucho
más sencilla que en el horno de ladrillos ordinario y el trabajo del
fogonero más simplificado.
7. La carga y descarga de ladrillos es cómoda y
fácil.
8. Si la arcilla y el esmalte son apropiados, pueden cocerse
tejas esmaltadas en una proporción de 85 % con relación al
total de la hornada.
9. Casi todos los hornos anulares pueden transformarse,
con poco gasto relativamente, en hornos apropiados para cocer tejas.
10. En tales casos no es necesario transformar de una vez todo el horno;
sino que basta empezar las pruebas utilizando sólo una parte, sin
perjudicar el servicio del resto.
El coste de la instalación de un horno Hotop, incluido un buen sistema
de humear, supera sólo en un 10 % al coste de un horno anular sencillo.
El horno Hotop es muy indicado para la cochura de artículos esmaltados.
Los hornos anulares con departamentos independientes (fig.
49) se utilizan para cocer artículos de calidad superior y constan
de varias cámaras contiguas en las que se lleva la cochura de un modo
continuo y según los principios que rigen el servicio de los hornos
anulares. La diferencia entre ambos tipos es debida a que los hornos con
departamentos independientes están formados por cámaras contiguas
separadas entre si por un muro; mientras que en el horno anular la separación
de un departamento no es permanente, sino accidental, y se hace por medio
de tabiques correderos de papel.
En los hornos con departamentos independientes se emplean combustibles sólidos
o gaseosos.
Ni en uno ni en otro caso hay contacto entre las piezas y el combustible.
Estos hornos tienen, pues, las ventajas del horno con llama de retorno y
la economía de combustible del horno anular.
Terminada la cochura en una cámara, se puede aislar ésta por
completo del resto y utilizar el calor latente de la misma para calentar
el aire empleado en la combustión de la cámara contigua. Cada
cámara es un horno de llama de retorno, con el hogar colocado a un
lado, y puede ponerse en comunicación con las cámaras próximas
y el conducto de humos por medio de registros y válvulas.
Fig. 49.- Horno anular con departamentos independientes.
La clase de hogar empleado depende de las mercancías
que han de cocerse y de las ideas del constructor. Actualmente se utilizan
hogares tipo gasógeno y semigasógeno. La duración de
la cochura en cada cámara depende de sus dimensiones y de la clase
de artículos que se cuecen. Esta duración es mucho menor en
estos hornos que en cámaras sueltas, pues se economiza el tiempo empleado
en humear y calentar las piezas al rojo.
Las cámaras se cierran con válvulas de arcilla refractaria
o por medio de registros. Estos cierres permiten aislar por completo cada
una de las cámaras y regular la cochura con entera independencia del
funcionamiento de las otras. En caso necesario se apaga una cámara
y se deja aislada. Un horno circular necesita doce cámaras.
Los hornos de cámaras independientes son apropiados para artículos
que necesitan una temperatura de cocción muy elevada, tales como ladrillos
recochos, refractarios, baldosas, materiales de consistencia pétrea,
productos inatacables por los ácidos y tubos.
El consumo de combustible es superior al de los hornos anulares, por ser
más elevada la temperatura de cocción; en cambio gastan menos
que los hornos sueltos, pues los de cámaras utilizan para humear y
cocer al rojo, el calor latente de las cámaras contiguas. Consumen
de 250 a 400 Kg de hulla por mil ladrillos normales, o sea de 10 a 30 % menos
que los hornos sueltos.
El coste es superior al de los hornos anulares, puesto que las paredes interiores
son de material refractario, a fin de soportar temperaturas elevadas de cocción.
Hornos Haederich.—
Su empleo es muy ventajoso para cocer ladrillos de revestimiento, barrococidos
y ladrillos de clase superior.
Los hornos anulares pueden transformarse fácilmente en hornos de tipo
Haederich. Las paredes se levantan bajo una línea de agujeros de la
bóveda, transversalmente a la cámara del horno y a dos metros
de distancia una de otra; se construyen de ladrillos refractarios y de seis
a quince centímetros de espesor. Entre las paredes se monta una rejilla
escalonada formada por material refractario, de dimensiones, inclinación
y detalles constructivos apropiados a la sección del conducto de humos
y a la naturaleza del combustible empleado.
El combustible se echa sobre la rejilla por los agujeros de la bóveda.
Las escorias y cenizas se depositan en el hueco situado bajo la rejilla y
comprendido entre ambas paredes. El aire para la combustión procede
de la cámara que se está enfriando y entra, ya caliente, por
una abertura lateral del cenicero; al atravesar la rejilla se pone en contacto
con el combustible y levanta llamas que penetran en la cámara, contigua
al hogar, a través de los agujeros practicados en las paredes, solera
y bóveda. Estas llamas envuelven los objetos que se están cociendo,
los endurecen y les dan un color uniforme.
Se puede producir un fuego horizontal en la cámara del horno,
abriendo una serie de agujeros colocados en la pared de salida de las llamas
y tapados por ladrillos sueltos. Es muy recomendable emplear esta disposición
cuando se transforma un horno anular antiguo que no tiene suficiente tiro.
La casa M. Franke, de Magdeburgo, construye estas paredes y hornos
del tipo que estamos describiendo.
Otro procedimiento para calentar los hornos anulares consiste en emplear
conductos de calefacción formados por los mismos ladrillos que han
de cocerse, o bien por ladrillos refractarios, y en este caso tienen un carácter
permanente. Estos canales tienen varias aberturas en la superficie y se colocan
verticalmente desde los agujeros de la bóveda hasta la solera, donde
enlazan con otros conductos horizontales colocados en dirección del
eje de la cámara.
HORNOS DE GAS
Son poco usados en las tejerías ordinarias; en cambio en las fábricas
de ladrillos de revestimiento, mercancías finas, ladrillos refractarios
y en general donde se elaboren productos que han de preservarse de cenizas
volátiles, cambios de coloración y otros defectos inherentes
a la combustión de materias sólidas, es ventajoso el empleo
de hornos de gas, ya sean circulares o de cámaras.
Fig. 50.— Planta de un horno anular de gas.
La experiencia y las pruebas realizadas han demostrado
que en estos hornos también pueden producirse cambios de coloración;
pues entre los gases que se queman se encuentran sales amoniacales, vapores
alcalinos y compuestos de azufre. Los hornos de gas no son, por consiguiente,
una protección segura contra malas coloraciones.
Horno de gas de la fábrica Schwandorf
(fig. 50).—
Este horno tiene la misma disposición que el horno anular de Hoffmann;
pero tiene además los conductos y válvulas necesarios para
la regulación y conducción del gas. El gas no se produce en
el mismo horno, sino en un gasógeno o generador de gas, desde donde
es conducido al horno. El gas afluye continuamente al horno y por medio de
válvulas se interrumpe la combustión en cualquier punto. El
fuego se puede repartir y regular mucho mejor en estos hornos que en los
de combustible sólido.
Fig. 51.—Corte transversal de un horno de gas.
El gas procedente del gasógeno llega a la solera
del horno pasando por unos canales de mampostería (sistema Escherich)
o bien entra en el horno por la parte superior, pasando por unos tubos desmontables
de plancha de hierro u otro material (fig. 51). En este último caso
las válvulas de paso están colocadas en la parte superior y
son muy fáciles de manejar. Las pipas p, p, o sea los tubos
de salida del gas son de arcilla refractaria, están colocadas entre
las mercancías y la llama sale desparramándose a través
del mechero. Los mecheros se colocan en los mismos puntos donde se levantarían
los conductos de calefacción en un horno circular. Las pipas se colocan
desde los agujeros de la bóveda, una vez se han dispuesto los ladrillos
en el horno; cuando ha terminado la cochura se sacan estando todavía
calientes. Tienen las pipas una serie de pequeños agujeros por donde
sale el gas en dirección normal al tiro, quedando así la combustión
uniformemente repartida en todo el horno. En la bóveda del horno hay
un pequeño agujero, colocado entre pipas, con objeto de observar la
marcha de la combustión. R es el conducto de humos que va a
la chimenea y r los registros en forma de campana.
Hornos de cámaras para combustibles gaseosos. —
Estos hornos se emplean para cocer a elevada temperatura, y por las razones
ya expuestas en párrafos anteriores. El tipo más conocido es
el de Mendheim (fig. 52).
Fig. 52.—Planta de un horno Mendheim.
El gas se produce en gasógenos usuales y difiere
del gas de alumbrado en que encierra los elementos secos y limpios de la
substancia empleada para producirlo, que no se han condensado en la separación
en seco; en cambio el gas de alumbrado se obtiene destilando carbón
y contiene principalmente óxido de carbono, mientras el cok queda
como residuo en la retorta.
Fig. 53.—Corte transversal del horno Mendheim.
El gas producido en los gasógenos a, a
llega a las cámaras a través de un canal de mampostería.
Unas válvulas f, f dan paso al gas para que penetre en la cámara
respectiva. En la solera del horno hay una serie de agujeros por donde penetran
gas y aire juntos. El aire empleado para la combustión pasa primero
por la cámara que se está enfriando y atraviesa luego los estrechos
agujeros de las paredes medieras adquiriendo una temperatura tan elevada
que, a su contacto, el gas se enciende inmediatamente y se desarrolla una
gran cantidad de calor en el horno. Las llamas procedentes de nueve cámaras
llegan a la última cámara de un lado pasando por las aberturas
correspondientes y van de allí a las cámaras diez y once del
otro lado. Esta última está separada de la cámara doce
por una plancha corredera y está enlazada, a través de un registro,
con el conducto de humos y la chimenea. En estos hornos se utiliza, como
en los circulares, el calor latente de la cámara donde ha terminado
la cochura, y el de aquellas donde todavía continúa, para calentar
previamente la primera cámara que ha de entrar en combustión.
El servicio adelanta como en los hornos circulares.
La conducción de estos hornos es sencilla. No es posible que se presenten
los defectos debidos a cocer rápidamente las piezas, puesto que las
llamas que abandonan el horno sólo permiten una elevación lenta
de la temperatura. Los hornos de cámaras para combustibles gaseosos
son muy recomendables para la fabricación de objetos de arcilla que
necesitan grandes secaderos, pues instalando éstos sobre el horno
se tiene una ventilación y calefacción gratuitas.
"Manual del fabricante de ladrillos"
Julio von Bük
Gustavo Gili, Editor, Barcelona, 1923